
Customers trust and buy products from those organizations that have proven their quality standards. Organizations around the world are trying to improve their daily business operations to outdo their competitors. Thus, by improving the quality of their business process, organizations can deliver high-quality products and services for their customers. Using this powerful root cause analysis tool, organizations can identify and rectify the problems that are creating quality issues for them. The fishbone diagram is a simple yet effective quality management tool that helps in root cause analysis. Only then, quality experts can brainstorm again and use other quality management tools to solve the problem and improve the business process of their organization. The process needs to be repeated until all the causes and sub-causes are represented in the fishbone diagram. If two cause categories have the same sub-causes that must be depicted in the diagram as well. Sub-categories are included to find the effects of the causes also known as sub-causes. Each bone represents the causes categories as mentioned above. The problem that the quality management professionals are trying to solve goes at the head of the fishbone diagram. Then, the fishbone diagram can be created using marking pens and whiteboards or through online tools according to their preference. Fishbone Root Cause AnalysisĪfter identifying the problems in the business process through brainstorming, quality management professionals create the final problem statement. This category is for the external factors that affect the general functioning of the business process like the temperature of the work area, storage conditions, and such. PeopleĪll the people or manpower that are involved or are associated with the business process are mentioned here. Quality standards or measurement units used in the business process are depicted in this category. The raw materials or similar resources used during the business process are represented under this category. This category is for all the elements related to the equipment or machines used in the business process. This category of causes is for documents and instructions during the operations of a particular business process where the defect has been found. These categories may defer according to the nature or domain of the industry however, the most used categories of causes are – Methods, Machines, Materials, Measurement, People, and Environment. Every cause and its potential effects can be depicted in the fishbone diagram under categories and sub-categories. Brainstorming with the quality management team and communicating every aspect of the business processes helps in finding the possible causes of the problem that they need to solve. Categories of Causes in a Fishbone Diagramĭuring the process of finding the potential causes of a specific problem, quality management professionals and quality experts are encouraged to ask as many “why?” questions as they can find. This root cause analysis tool also helps in brainstorming and finding the right solution to eliminate the problems faced by the organization. Thus, a visual representation of the problem and its potential causes helps quality management professionals who are working to solve the problems in the business process of their organization to successfully identify the root causes of the problem. In the diagram, the head of the fish depicts the problem, and each bone of the spine depicts the potential causes of the problem. Later, it was nicknamed the fishbone diagram due to its similarity with the skeleton of a fish laid on one of its sides.Ī fishbone diagram is also known as the cause-and-effect diagram, as it helps in finding the root cause of the problem in the business processes of an organization. This quality management tool was named the Ishikawa diagram in honor of its creator.
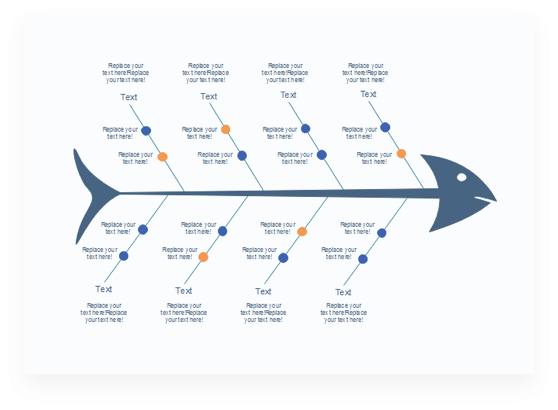
Kaoru Ishikawa is known to use the fishbone diagram for the first time while working with the Japanese company of Kawasaki. At the time, Japan was re-inventing its manufacturing and automobile sectors by introducing the concept of quality management in regular business processes.
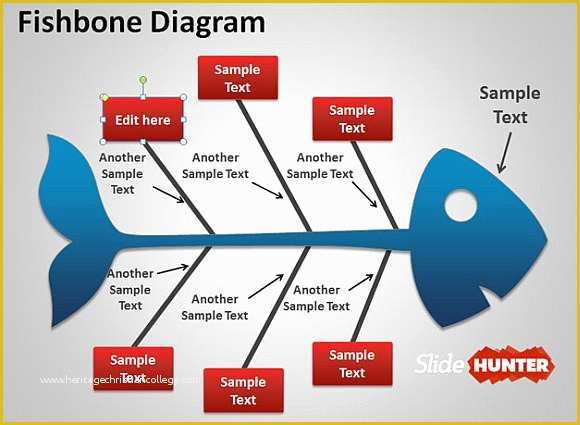
The Japanese professor at the University of Tokyo, Kaoru Ishikawa invented the fishbone diagram in the 1960s. Categories of Causes in a Fishbone Diagram.
